Due to much need for cement in basic and also house and building construction projects in Iran; AzarAb has wide activity in planning, manufacturing, and erection and commissioning of cement and plaster (Gatch) plans. AzarAb started planning the cement plant in cooperation with F. L. Smidth from Denmark and Loesche from Germany. AzarAb has done the work of engineering, production, erection, and commissioning by itself. Shahre Kord cements plant with 3300 tons/day is a prominent sample; in which planning, manufacturing, erection, and commissioning of the work. This project is passing its final steps in erection and commissioning nowadays. (Pictures 1 to 9)
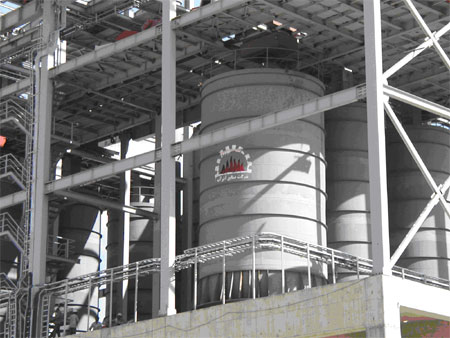
1. Cement Mill Bunkers – Shahre Kurd Cement Plant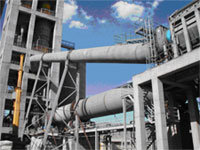
2. Furnace and Third Air Duct– Shahre Kurd Cement Plant
3. Material Mill Feed Bunkers– Shahre Kurd Cement Plant
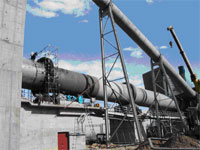
4. Furnace and Third Air Duct Shahre Kurd Cement Plant
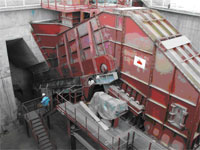
5. Crusher– Shahre Kurd Cement Plant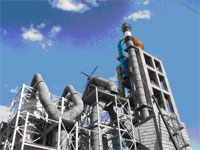
6. Material Mill and Pre-Heater– Shahre Kurd Cement Plant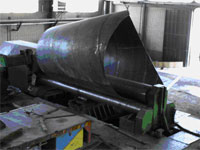
7. Making Cement Plant Parts– Cement Site
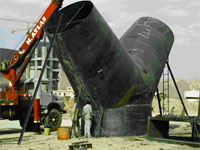
8. Making Parts of Shahre Kurd Cement Plant
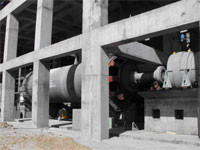
9. Cement Mill– Shahre Kurd Cement Plant
AzarAb has manufactured the furnace, cooler, raw material mill, cement mill, and crusher of Mazandaran, Kerman, Kangan, Tehran, Kerman Momtazan, Ilam, Abyek, Jovin, Khozestan Ekbatan, Sardar, Urumiyeh, Bojnord, Mazandaran cement developing plan and Khorasan plaster plant. Planning, manufacturing, erection and commissioning of Tabas, Tafresh and Sabzevar with 3300td capacity is completely committed to AzarAb that has started their performing now.
Cement Production Process:
Limestone that forms 75% of cement raw material is extracted from min and transferred to crusher. It crushes the stones up to 12mm size. A belt conveyer transfers them to mixing hall and stacker collects them. Reclaimer will pick up from these storage hills and by falling them on a belt, conduct them to feed bunkers of raw material grinding plant. There are three to four bunkers in this unit. One of them is for limestone and other are for the material containing proper proportions of calcium, sillies, aluminum and Ferro oxides that normally are ferrous and clay. Here, limestone and other material mix with each other in some special portions and send to raw material grinding plant. This unit -that contains some rollers- powders the raw material and sends them to duct ended to separator cyclone. In cyclones, by centrifugal force, material separate from air and transfer to silos by air slides. Blowers in silos will homogenize material. Then material will be sent to pre-heater upper part. There, outlet hot gases preheat them in some phases. They will come down the pre-heater due to their weight. Here the cold and hot air direction is vice versa. Then material enters the rotary kiln and cure. At first calcium carbonate will be turned to calcium oxide by freeing the carbon dioxide. Then calcium oxidized will form other calcium silicates and aluminates with other combinations. The outlet production from the furnace will be poured to cooler to be cooled down. Last material will be as granulated black clod called as clinker. These clinkers will be sent to clinker silos by Aumund band. Then clinkers is sent to cement mill and mixed with a low proportion (about 4%) plaster. The mixture Powders by ball mill that is called Cement. The produced cement will be sucked by fan and send to separator. In separator, the powdered cement will be separated and sent to cement silo and or loading house. To prevent air pollution, outlet gas will be filtered by electro filter before entering the stack. Some magnetic plates absorb dust. The entering gas is filtered consequently, and dust will collect in bag filters. An electro-filter exists for each of furnace, cooler, raw material mill, and cement mill units. (Schematic figure 1)
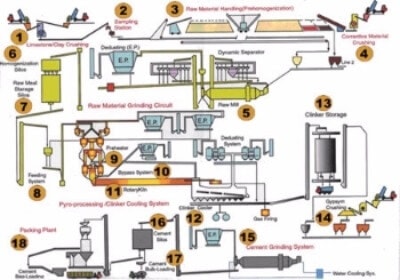
Figure 1: A Complete Cement Plant Plan
1- Crusher (Limestone) 2- Sampler 3- Mixing Hall 4- Crusher (Clay)
5- Raw Material and Electro Filter 6- Congenial Silo 7- Pre-Heater Material Feed Silo
8- Material Transfer To Pre Heater System 9- Pre Heater 10- Regulating Air Duct
11- Rotary Kiln 12- Cooler and Electro Filter 13- Clinker Silo 14- Plaster Feed
15- Electro Filters And Cement Mill 16- Cement Tower 17- Bulk Loading 18- Loading House